Who is Hoosier Energy?
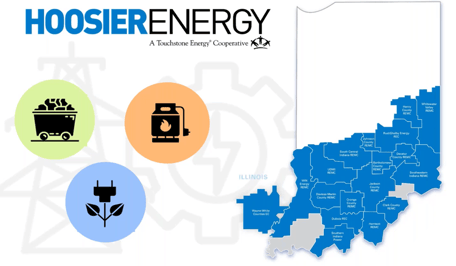
Hoosier is a Generation and Transmission electric cooperative providing wholesale power and services to 18-member distribution cooperatives in south-central Indiana and south-eastern Illinois. Founded in 1949, Hoosier serves more than 300,000 end-customers across nearly 1,700 miles of transmission lines.
Hoosier Energy takes an “all of the above” approach to generation resources with a mix of coal, natural gas, renewable energy resources. And in 2023, the utility is scheduled to retire its last remaining coal plant in Merom, IN.
Stop the Chaos!
Unlike many utilities where tribal knowledge is lost when their aging workforce retires, Bernie Voges, Senior Protection Engineer at Hoosier Energy, had the good fortune to work next to people who’d been at Hoosier for 42 years. While he gained a deep knowledge from his predecessors, he also saw the huge downside to working without an automated drawing management system. In a word, it was chaos.
~ The Utility’s hundreds of thousands of paper drawings and documents were all being stored in Windows folders.
~ People were copying out files into their own hard drive to work on and then putting them back on the network – anywhere.
~ Files were overwritten, accidentally moved, and even sometimes accidently deleted and unrecoverable, so work had to be recreated from scratch.
~What had been manageable with a couple of designers, became completely out of control as more engineers came onboard, and 3D models and concurrent work processes were introduced.
~There was a deluge of printed paper circulating through field services. It was common to have two different drawings with the same version number. The results were some grave mistakes.
In fact, Bernie recounts a mishap that sounds absolutely implausible and comedic—if it wasn’t true.
“A contractor in charge of all the ‘demo stuff’ went on site, and based on his print, rips out all of the equipment. A second contractor enters the same site, reads his print and re-installs conduit cables. Next day, the first contractor returns, sees the cables and stuff, and thinks he's missed something from the day before. So, he rips everything out again.”
The situation is funny to recount, says Berne, because no one was hurt.
But, he cautions, when it comes to the protection side of things, there’s a lot more at stake.
“When dealing with relays and stuff that control the wider bulk electric system, if someone has an old version of a drawing and puts one wrong wire in one wrong place, you’re looking at a whole huge substation blackout or worse . . .and people are getting damaged or hurt.”
Bernie’s been at Hoosier since he graduated from Purdue, first in the substation design department and now in protection controls. In addition to his engineering workload, he’s responsible for the administration of all CAD products and compliance with NERC/FERC reliability standards.
He’s also been at the helm of Hoosier’s multi-year journey to automated engineering drawing management. Young and unusually patient, Bernie knew he would, simply said, outlast the naysayers.
One Door Closes; Another Opens
In 2009, Bernie saw an opportunity to make a pitch to upper management for a drawing management system. Hoosier Energy was bringing on a new Co-op member and needed to add a few thousand more drawings to the network for new substations and transmission lines.
Bernie remembers his presentation as a “swing and a miss”. He was told that “everything was just fine as is, and Hoosier didn’t really need a system.”
Two years later, when the power plants approached IT for “some drawing management solution” IT suggested they, ‘go talk to Bernie’.” The idea for an automated drawing system was resurrected
This time around, Bernie changed his tact. He created a core team of people to evaluate and develop requirements for an EDM system. The team consisted of “Power Users” and other key players from the Records Retention Group, Engineering, and Operations on both Transmission and Generation Plant sides.
He knew the different cultures of the generation and transmission sides of the business was an important consideration. On the generation side, people were change-resistant and preferred the status quo when it came to operating the plant. Most of their design work was outsourced, and new power plant construction was light. On the transmission side, they was responsible for a large and diverse geography throughout the state, where new transmission lines, substations, renewables were regularly emerging. Almost all transmission design work was done in-house.
In addition to the two very different business ways of thinking, Bernie wanted to avoid a repeat flop from a former CMMS implementation. “I wasn’t on the initial implementation team, but I was part of the team that was developed to help fix it. I was able to take a lot of those lessons learned and apply them to our engineering drawing management project.”
The core team focused on how and who the new drawing management system would impact. Explains Bernie, “We had open and honest discussions about what we were doing, how we were doing it? Who's getting close to retire? Do we have to train new people?”
It took the core team close to two full years to develop an RFP. Then the hard work began: Identifying the right partner.
The Challenge of Selecting a Vendor
Because engineering drawing management wasn’t a core competency at Hoosier Energy, they wanted vendors to understand the Utility’s expectations and experience.
One thing was essential: Hoosier Energy wanted more than just software and services. They wanted a partner that would help them solve the issue of getting the chaos under control.
They developed a scorecard to outline their evaluation criteria. It included scoring weights for ease of use, ease of legacy import, quality of the project team, customization, technical support, training, and licensing. (See graphic below)
As part of the RFP process, all vendors were asked to deliver demonstration videos of their software using a subset of Hoosier’s data.
“We gave the vendor demonstration videos to our users so they could help us evaluate all the different bids,” says Bernie. “We wanted our users to see a solution working with our data to determine if they could ‘see themselves’ using the software and which one(s) they liked or considered terrible.”
Another key criterion was the quality of the vendor’s project team. Hoosier wanted a partner who had experience with drawing management and some understanding of working with utilities. “Being in the utility business,” says Bernie, “there's a lot of idiosyncrasies. We like to keep things the way they and are very hesitant to change. We wanted vendors to understand our culture and our preconceptions.”
An additional prerequisite was zero customization. “We wanted to keep the system as out of the box as possible to avoid the expense of maintaining and supporting any custom programming,” remarks Bernie.
Good support was just as critical. “As part of the RFP, we asked vendors to give us their normal business operating hours and their after-hours support. We also wanted to understand what online support capabilities they ha--like a Forum or FAQ --to help us solve our own problem before we called in the cavalry.”
After all the demos and the scorecards were tallied, the core team selected Synergis Adept.
There were several key factors for choosing Adept explains Bernie.
First, Adept provided flexibility for both divisions. Users felt it was easy to use and would “stay out of their way.”
Adept’s version control also did a great job as a “police cop”. It made sure that that everyone had the right version of a drawing—all the time.
“Another big selling points was that Adept didn’t encrypt our data,” emphasizes Bernie. “Adept kept our documents in their native format so if we did need to turn a 180 and choose a different vendor, it'd be very easy for us to do.”
Synergis’ support, the quality of their technical experts, and the simplicity of the solution all played into the decision to implement Adept.
With the vendor selection complete, there was one more big push: Getting the system in place and gaining user adoption.
Implementation from Start to Finish
One of the key tenets of the Hoosier implementation--beyond the stated requirements in the RFP-- was “don't repeat the mistakes of our CMMS implementation.”
“We wanted to be methodical, slow, and to keep things simple,” explains Bernie. “We also wanted to make sure the system worked for us and worked our way, without having to adjust our processes to conform to the software. At the end of the day, we wanted Adept to be easy for veteran engineers and our maintenance folks to learn so that we increased our end user buy-in, and the overall project success.”
Part of the implementation was unifying all the sites and the different generation facilities onto one server. Thankfully, Hoosier had a dedicated fiber optic network to all their disparate, remote sites for maximum speed and low latency.
A large effort was identifying all the different users, their profiles, and all the types of roles and level of access they needed. Says Bernie, “We asked ourselves, ‘who are power users? Who's going to be doing drawing approval?’”
To gain familiarity with Adept, the core team, along with administrators from Emergency Preparedness (EP), participated in administrator training.
“The Administrator training helped the team become familiar with the system and prepare them for the configuration stage of the implementation. The goal was to keep the configuration as simple and out-of-the-box as possible, while fitting their needs.”
They also spent time examining the metadata for miscellaneous documents such as Excel lists of network files and files from a 1990s MS-DOS-based database system.
The bulk of remaining legacy data were hundreds of TIF and PDF files. With the huge quantity of raster and image files, Hoosier contracted Synergis to do the work of extracting the metadata from the title blocks and writing it into the Adept database.
The final step was to migrate the rest of Hoosier’s disparate data into Adept, using different software rules to move things into the right place. It took one week, and the migration was complete.
Once user training was complete, people started working in Adept, checking in and out files.
Reflecting on the work they had accomplished; Bernie was pleased that the transition had been seamless.
The Never-Ending Benefits from Adept
Even after 11 years, Bernie can easily list off Adept’s benefits. Here is Hoosier’s “Top 8” list of high value advantages:
- Finding the right information at the right time from anywhere. “If you’ve ever done a search in the search bar of Windows Explorer through 250,000 files, it's going to take you a minute or two or longer. With Adept, it takes a second to parse through 20,0000 or 55,000 files and find exactly what you need.”
- Integration with Autodesk products. “Hoosier Energy is an AutoCAD shop and has been for decades. We use vanilla AutoCAD and AutoCAD Electrical. AutoCAD files have different XREFs—whether it’s a raster or image or it's another drawing it references. Adept does a great job of maintaining those existing references and keeping them from breaking.”
- Efficient drawing management in Inventor. “In the screen shot below, the Adept Task Pane inside Inventor is on the left. Hoosier’s substation design engineers really lean on the Adept Task Pane to get their work done.”
“We’ve also added a field in the modeling information for Substation stock numbers, which matches the exact maximum number for each item we store in house. If a designer needs to grab an insulator or a piece of a switch, they simply search the ‘maximum number’ field inside of Adept, pull up the model from the parts library, and drop it into the model. That extra data lets us generate a bill of material from within Inventor. We can get that list to our storekeepers, and they can start pulling things off the shelves and staging it for the job. It’s a very efficient use of drawing management.”
- Version control is key. “It makes sure that everyone has the right version that they need. That includes all of our static documents, such as easements, our property records, and our landowner agreements.”
- Adept is easy for people to learn and use. “It stays out of the way and lets people do their job. When users check a file out of Adept, it goes into your work area, which functions a lot like Windows folder, so it’s a familiar way of working.”
- Adept is a very cost-effective solution. “We actually finished the implementation way under their initial budget, because of Adept’s flexible licenses. Users work with Adept Explorer in a browser for searching and viewing. For creating and editing in CAD, the desktop client is ideal.”
- Adept integrates with our existing workflows. “We let people continue to do work as they were accustomed, which in turn has increased user adoption.”
- Synergis has top notch support. “If there’s a problem, I can call support on the phone, send 'an email, or submit an online ticket.”
Adept’s True Value: “We Couldn't Afford Not to Use it”
Bernie captured the good and hard lessons learned during the long selection and implementation process. Make no mistake. These lessons are the real gems; the not-to-be-overlooked experiences that anyone considering an engineering drawing management system should consider. Think of these as free consulting from an experienced peer. Something you’ll cherish when it’s your name on the line.
Adept is the single source of truth. It’s the one place to go no matter where you are in the company, it’s where all of our design drawings are. With that comes improved drawing access where all the different sites are now consolidated into one. Access is also available to anyone who asks -- whether someone in the accounting group or the billing group or member relations group, if they need access to the drawing files, they have easy read only access to it.
Upfront planning is crucial. “By having honest assessments with individuals, with our different departments we were able to come to probably the thing that would work best for us may not be the best way, but it was our way also. Plan in ways to improve workflows for the future.”
Don’t attempt to have software fix poor processes. “People always evolve workarounds to poor processes because it’s not used to what they're doing. Instead, put your plan into place and gradually introduce new changes whether to your workflows or different standards. It helps walk through people to be more efficient.”
Standardize your library structures. Make it easy for people to navigate. We devised top-down approach similar to our folder structure in our CMMS system. We used the equipment hierarchy to make it easy to navigate to a specific piece of equipment, pump. relay or a breaker.
Standardize group workflows. Use Adept’s workflows to create, check, and approve drawings. We have different work groups using different workflows. We also use workflows for our outside contractors. We give them a VPN access to our system and it's as if they're sitting at the desk in our office. Even though they're remote, they have access to all of our drawings and check them in for us to approve.
Eliminate duplicates. Duplicates are the unknown unknowns. You don't know about them, but you’ve got to plan for them. Make sure that you have a plan to fix them both in time and in money. We had a line item in our budget for contingencies to deal with some of this cleanup work.
Allow for adequate training and keep it simple. You want to make sure that, that you're not really forcing all the end users to drink from a fire hose. Keep it simple and make sure you listen to them. Otherwise, they develop their own workarounds and just undermine everything that you've worked for.
Use Transmittals to save time. Before Adept, engineers always developed “cover pages” to our Drawing Deliverables in Excel, where everything had to be typed in manually. Adept’s Transmittals helped us accomplish the same task with fewer clicks, and without manual data entry.
Capture tribal knowledge in a centralized file structure. We also instituted best sharing practices -- whether it's one design group or different sites in different facilities.
You can learn more from Bernie in one of these on-demand webinars, hosted by Synergis Software.
How Hoosier Energy Transformed Design Engineering with Adept
A live panel with Engineering and IT leaders from Eversource, Hoosier Energy and Great River Energy
Let us know how we can want help with your own document management challenges.
Schedule a meeting with an expert today.