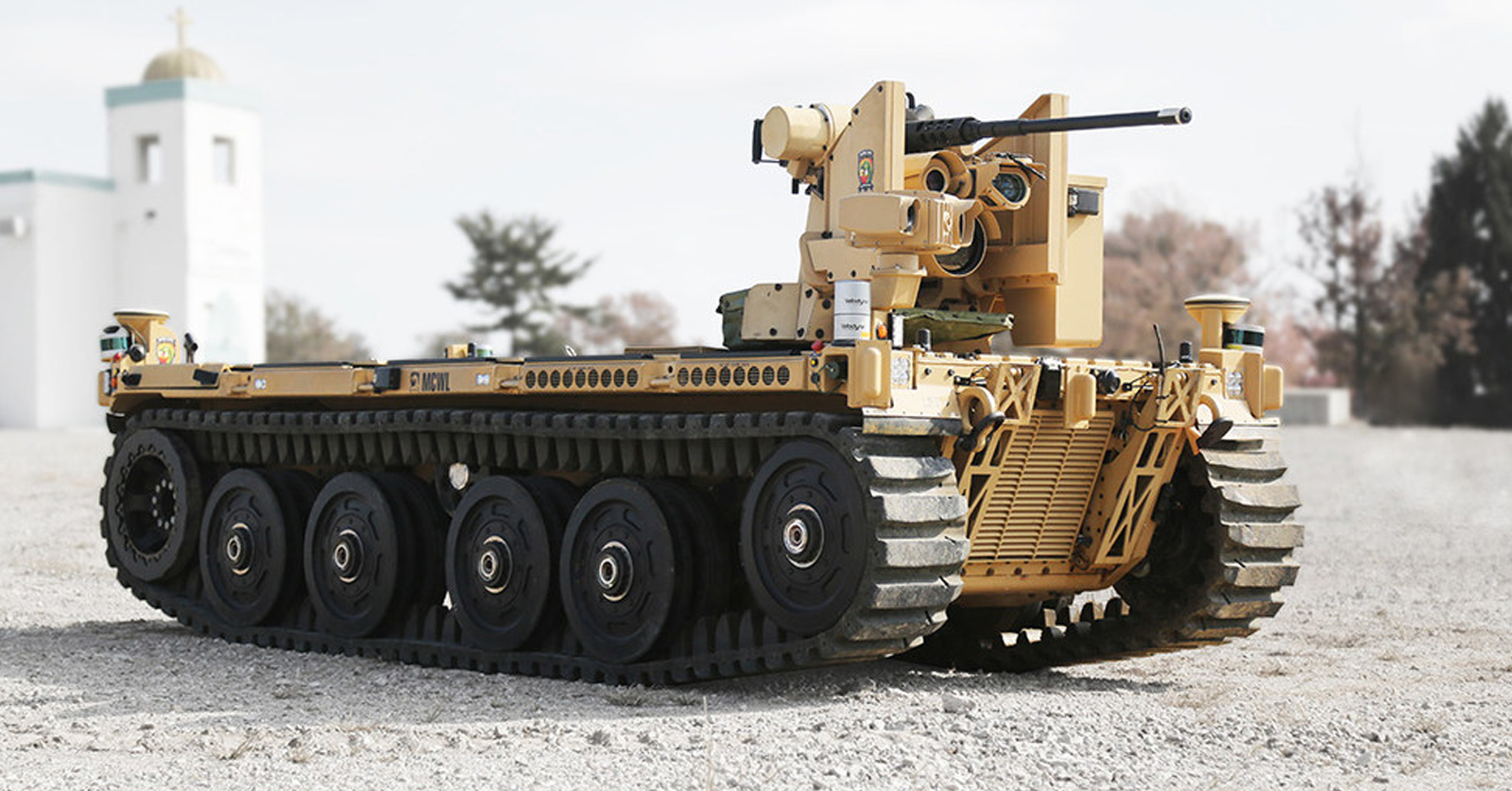
QinetiQ Relies on Adept Engineering Document Management to Manage Large Complex Projects and Achieve Industry Certifications
Company overview:
QinetiQ offers world-class expertise in advice, test and evaluation services, and innovative technology-based products. They use scientific and technological knowledge, proven research capabilities, and unique, purpose-built facilities to deliver services and products to meet the needs of a wide range of global customers. They operate primarily in the defense, security, and critical national infrastructure markets.
Goals
- To design, build, deliver, and support a portfolio of industry-leading products and engineering development that has been used and tested for decades.
- To provide a mission-led approach to innovation, which ensures the best capabilities get into the hands of warfighters and first responders when required.
- To achieve better processes, reduced costs, time savings, higher productivity, and the elimination of all labor-intensive processes.
- To automate as much as possible –without hiring additional personnel to support new processes.
- To focus resources on creating world class design solutions using a seamless process that secures, manages, and controls all project lifecycle documentation, with fewer people, manual processes, errors, and waste.
It’s one thing to reduce our costs and make us more efficient, but we also need to be able to measure the results. Our goal is to automate as much as possible without adding on more people. . . we need to make sure that a process is driving down cost for our customers or speeding up time to market, or both.
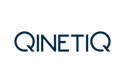
Challenges
- The company had rudimentary and labor intensive processes for document management— they used Microsoft Windows to assign rights to personnel and directories. Their systems would not satisfy the industry quality certifications they sought.
- It took work to change the culture of resistance to use an institutionalized document management system.
- They worked on complex and challenging projects that have strict development requirements. It required QinetiqQ to fully commit to improving their design processes. They needed good control and easy accessibility to their design products.
- They also required a reliable way to route material for review; and validate who reviewed and approved.
- Engineers maintained their document numbers on a spreadsheet, an awkward process that required many steps to obtain and number a document. And once in a while numbers would be overwritten and cause problems.
Paper creates a configuration management nightmare. With Adept, no one is asking ‘do I have the right version of the drawing?’ ‘Did we get that in the ECR?’ The version in Adept is the gold standard.
Solution
- Provides a flexible system that is part of an individual’s daily activities, rather than being an additional task.
- Manages simple or complex processes
- Ensures customers receive the right version during frequent documentation cycles.
- Links ECOs to the part baseline to improve the ECR process.
- Helps achieve and maintain critical audits.
- Tracks revisions and manages the inter-relationships between parts and assemblies in complex 3D CAD models with many thousands of discrete parts.
- Eliminates paper and controls versions on the manufacturing floor.
- Reduces gaps in approvals, resulting in dramatic reductions in time for outstanding signatures.
We relied heavily on Adept to achieve our goals of becoming a CMM level 3 and AS9100 company. If anyone has lived through an SEI CMM assessment, they know that the assessors do not enjoy struggling to find artifacts.
With Adept, our project forms, locations of an SOP, or document approval status or flow, is just a search away.
Results
- Provides continuous feedback to and from management to maintain constant improvement.
- Secures and maintains certifications in National Quality Aerospace Assurance for ISO9001, ISO AS9100, Software Engineering Institute (SEI) Capability Maturity Model level 3 (CMM 3), and Capability Maturity Model Integrated (CMMI) level.
- Integrates with the company’s process improvement charter, along with Lean Six Sigma tools.
- Manages the review and release processes for over a hundred performance specifications requiring peer reviews.
- Eliminates errors for greater efficiency and competitiveness.
We’ve just about eliminated the errors we had before. In today’s ultra-competitive world, companies can’t afford to be inefficient. Adept ensures we are efficient.